PCB沉金工艺流程简介预浸
- 发布时间:2025-05-23 15:57:06
- 浏览量:394
以下是PCB沉金(ENIG)工艺中预浸(Pre-dip)步骤的详细说明,作为前处理流程的关键环节之一:
预浸(Pre-dip)的作用
-
保护铜面:
在酸洗和水洗后,铜面处于高度活化状态,极易氧化。预浸通过覆盖一层保护性溶液(如稀酸或络合剂),隔离铜面与空气接触,防止氧化。 -
调节表面pH值:
沉金药液(如化学镀镍液)对pH值敏感,预浸液可将铜面pH调整至与后续药液兼容的范围(通常为弱酸性),避免因pH突变导致镀液失效。 -
去除残留杂质:
进一步清除铜面残留的微量污染物(如金属离子、有机物),确保沉金反应均匀性。
预浸操作参数
-
药液成分:
-
常用稀硫酸(H₂SO₄,5-10%)或专用络合剂(如柠檬酸、EDTA)。
-
部分工艺采用与沉金药液成分匹配的专用预浸液(含稳定剂)。
-
-
pH控制:
-
通常为pH 2-3,需与后续化学镀镍液的pH(4-6)平缓过渡。
-
-
温度与时间:
-
室温操作(20-30℃),浸泡时间1-2分钟。
-
对高密度板或盲孔结构,可延长至3分钟以确保孔内润湿。
-
注意事项
-
避免污染:
-
预浸液需单独使用,严禁混入其他槽液(如酸洗液或水洗残留)。
-
定期更换预浸液(如每班次或根据生产量),防止杂质积累。
-
-
时间控制:
-
预浸时间过短:铜面保护不足,易氧化;
-
预浸时间过长:可能引入酸液残留,干扰后续镀镍反应。
-
-
水质要求:
-
预浸后需用DI水(去离子水)喷淋,电导率≤5 μS/cm,防止杂质污染镀镍槽。
-
-
流程衔接:
-
预浸后需立即进入化学镀镍槽,避免铜面暴露在空气中(建议间隔<30秒)。
-
预浸异常问题与对策
问题现象 | 可能原因 | 解决方案 |
---|---|---|
沉金层局部发黑 | 预浸液污染(如金属离子) | 更换预浸液,加强水洗和过滤系统 |
镀镍层结合力差 | 预浸后铜面氧化(流程中断) | 优化流程衔接,缩短预浸至镀镍时间 |
孔内镀层覆盖不全 | 预浸液未充分润湿盲孔/微孔 | 增加预浸时间或添加润湿剂 |
沉金药液pH波动 | 预浸液pH与镀液不匹配 | 调整预浸液pH至工艺要求范围 |
预浸效果验证
-
目视检查:
-
预浸后铜面应保持均匀粉红色,无氧化斑点或水渍残留。
-
-
接触角测试:
-
使用水滴角测试仪,铜面接触角应≤10°,表明表面清洁且润湿性良好。
-
-
沉金层附着力测试:
-
通过胶带剥离试验(如IPC-650标准),确认镀层无脱落。
-
总结
预浸是连接前处理与化学镀镍的“桥梁”,其核心在于:
-
防氧化:保护铜面活性;
-
调pH:确保镀液稳定性;
-
去残留:提升沉金均匀性。
需通过严格的过程控制(pH、时间、水质)和定期维护,保障沉金工艺的可靠性。
免责声明:部分文章信息来源于网络以及网友投稿,本网站只负责对文章进行整理、排版、编辑,意为分享交流传递信息,并不意味着赞同其观点或证实其内容的真实性,如本站文章和转稿涉及版权等问题,请作者在及时联系本站,我们会尽快和您对接处理。
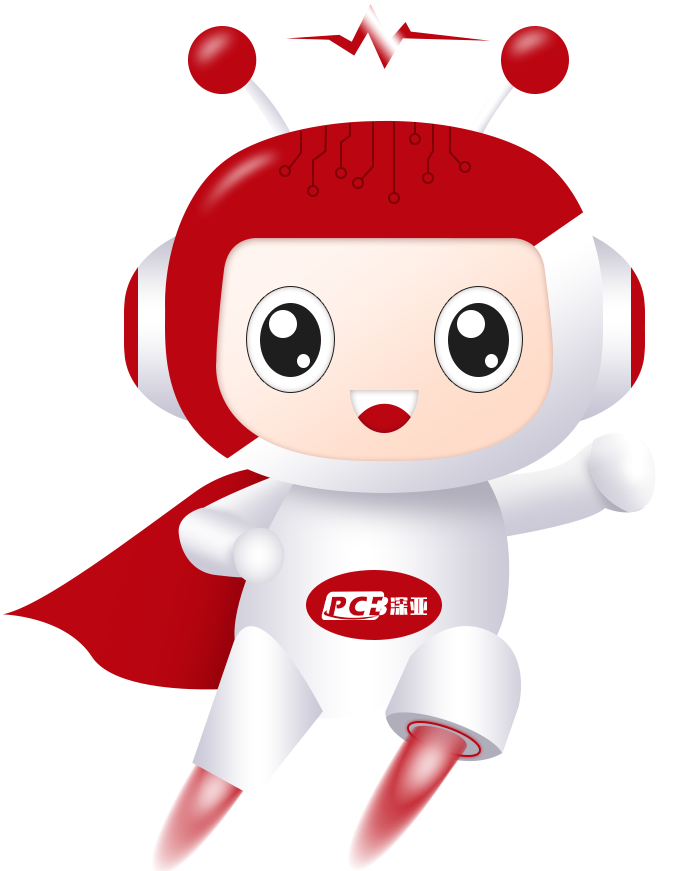